How Prefabrication Enhanced Sustainability and Resilience at Baptist Hospital

By Brian Griffis
The designers of the new Baptist Hospital campus in Pensacola, Fla., knew the facility had to be resilient. After all, the very need for the hospital was the result of a natural disaster.
When Hurricane Ivan hit the Florida coast in September 2004, it left an indelible and enduring mark on the face of Baptist Health Care’s E-Street campus. In the years that followed, a compromised building envelope and frequent, costly interruptions to operations created lingering problems for the healthcare facility.
Challenged by a facility that could no longer meet its evolving needs, Baptist Hospital began developing a new $636 million health campus on a 57-acre site. The campus would ultimately include a new 10-story, 264-bed hospital, a six-story, 178,000-square-foot multispecialty health center, an 80,000-square-foot developer-owned medical office building, a 48,000-square-foot behavioral health hospital and a 23,000-square-foot central energy plant.
Above all else, the campus needed to withstand future major weather events while achieving sustainability goals, as the region has seen an increased frequency of storms such as Ivan and others due to climate change, according to the Center for Climate and Energy Solutions.
The SolutionThe owner desired a hospital that could remain operational during and after significant weather events, specifically a design that could support seven days of off-grid operational capacity and withstand a 1,000-year storm—a Category 5 hurricane with up to 200 mph wind speeds.
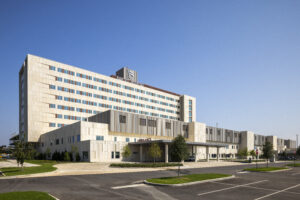
The project team chose prefabrication because it provided a robust and resilient hospital with the durability and strength to handle future extreme weather events. Additionally, prefabrication offered unprecedented levels of sustainability and greater control over schedule, quality, safety, predictability and cost.
Many of the hospital’s components—patient and staff bathrooms, medical headwalls, hydronic piping and building envelope—were prefabricated offsite, reducing overall construction waste by 83.2% and energy use by 67%.
Early CollaborationFor the building envelope, the designer chose an architectural precast facade system as the optimal material to represent the sustainability design narrative. The prefabricator, GATE Precast, collaborated with project architect Gresham Smith and general contractor Brasfield & Gorrie early with a design-assist approach to meet the demands of a compressed schedule and offered multiple facade types and architectural finishes to complement the overall design intent, blending the architecture and interior design seamlessly together with simulated materials such as terracotta, wood, bronze and terrazzo.
The designer selected a lightweight, thin unitized architectural precast concrete (APC) system for the facades of the main hospital and health center towers and a 6-inch traditional insulated APC system for the tower podiums. The product’s flexibility allowed the design team to work with the prefabricator to affordably and attractively incorporate emulated terracotta accents and limestone finishes to create varying shades of color and a random appearance within the panels, lending depth and a timeless appearance.
Sustainability AchievedThe selection of the facade systems significantly contributed to the hospital’s sustainability profile. The project team reduced the structures’ carbon footprint by more than 70% by specifying a single source unitized concrete façade envelope, complete with glazing and insulation, that was fabricated offsite, constructing a complete thermal, vapor and air barrier system to withstand the elements.
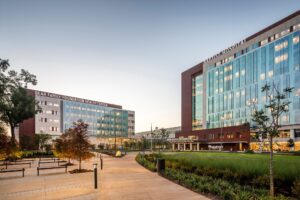
A unitized system also reduced enclosure times and job site disruptions by eliminating traditional trades from the site, accelerating the schedule by five months and minimizing environmental impact. That came with the additional benefits of reduced trades and equipment on site, faster dry-in of the building envelope, improved quality control on the ground prior to panel installation and performance testing of panels before installation.
The 2.25-inch-thick lightweight prefabricated panels also required significantly less concrete, reducing CO2 emissions. Concrete use was reduced by 70% compared to traditional precast panels. For the medical office building portion of the work, a traditional 8-inch precast concrete panel system would have required an additional 322 cubic yards. And for the hospital, it would have required an additional 998 cubic yards. More than 1,000 transportation miles were saved by hauling the glazing to the precast manufacturer’s facility rather than to the job site.
The system included a host of other sustainable attributes:
- The structure of both the hospital and health and wellness center utilized Type 1L cement for the beam and slab mix, which contributed to a 13% reduction in embodied carbon compared to an alternative mix.
- The tube steel used in the lightweight panel mainframe includes 90% recycled content.
- The lightweight panels are coated with an HFO spray foam insulation with an ultra-low GWP (Global Warming Potential) and high R-value of 7.5 per inch, which reduces the amount of energy required to heat and cool the building while also lowering energy bills and subsequent greenhouse gas emissions.
Overwhelmingly, the lightweight and traditional prefabricated systems helped meet the project’s sustainability goals by reducing waste and energy throughout the construction process and improving storm resistance. As a result, with a planned 75- to 100-year lifespan, the new campus, opened in September 2023, stands ready to serve the community under even the harshest of conditions.
Brian Griffis has more than 25 years of experience in the construction industry and serves as vice president of sales for Gate Precast, which joined The Wells Companies Inc. in 2024. Griffis attended Florida State College at Jacksonville prior to spending four years as an Army Ranger. Additionally, he served as chairman of the PCI Architectural Precast Committee.
hconews